Primer Welds Safety and Steel
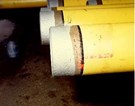
As a leading innovator in advanced technology for corrosion protection of pipe, fabricated piping, structural steel, pilings, and tanks, a large fire protection division of a general steel company leaves no stone unturned to provide their customers with clean corrosion free welds.
To suit their rigorous standards, Standard Pipeprotection of St. Louis, MO selected a pre-weld primer known as Bloxide from Tempil Inc., South Plainfield, NJ. Bloxide is a "de-oxidizing" weldable primer that is brushed directly on pipe sections and other critical weld joints prior to shipping fabrications to the field for erection.
Bloxide is a pre-weld treatment that has no objectionable compounds to contaminate weld areas. Bill Moore, area manager for Standard Pipeprotection reports that, "once applied, [Bloxide] does not have to be removed for welding. Other rust preventive coatings, including coal tar primers, have to be cleaned off to prevent contamination in the weld joint."
All field joints contain some oxygen in the form of rust or moisture. Aluminum flake in the Bloxide serves as a de-oxidizer, improving the weld quality in carbon steel. Oxygen has an affinity for aluminum and forms aluminum oxide. Therefore, pinholing and porosity is eliminated.
The compound can be brushed, dipped, or sprayed at the original weld preparation, and prevents rust during the time before actual welding occurs. It may be welded over immediately after the coating has been applied.
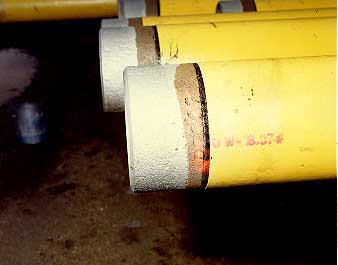
The weldable primer withstands extreme working temperatures as high as 800° F, making it suitable for high temperature work in refineries and chemical plants. The primer is effective on all steels, and is free from lead, sulfur, zinc, cadmium, mercury, and halogens. As a halogen-free primer, it has particular application to industry and government standards - NACE, AWWA, ASTM, NAPCA, SSPC, DOT and the Utilities Nuclear Coating Work Committee.
In field tests, Bloxide retained its integrity and exhibited no corrosion. After 12 months of outdoor exposure, no adverse corrosion was apparent. In addition, testing conducted at Tempil's laboratory yielded the following results:
- Immersion in water at 70° F for 200 hours: the coating retained its integrity and the steel substrate exhibited no corrosion. After two months of immersion in water at 70° F, small hard blisters appeared, but the integrity of the coating was maintained.
- Immersion in artificial seawater (3.2% brine) 70° F: small hard blisters on coating, but no other effect.
- Heat resistance at 842° F: coating remained virtually unchanged.
For more information about the product, contact Dennis Redline, business development manager for Tempil Inc., 2901 Hamilton Blvd., South Plainfield, NJ 07080; Telephone: 800-757-8301; FAX: 908-757-9273; E-mail: tempil@tempil.com. Tempil is one of the world's leading suppliers of temperature indicating products and protective coatings for a wide range of applications in the welding, heat treating, and electronic industries.