Lazzara on Safeguarding: An organized workplace - the foundation for safety
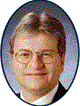
I was first introduced to the Japanese 5S process several years ago when one of our executives returned from a trip to Asia. I rediscovered the process during a conversation with guest columnist Mike Taubitz, who discussed the positive experience he has had utilizing the 5S procedure emphasizing safety in an organized workplace. Mike is the Global Health and Safety Regulatory Liaison for General Motors, and agreed to share his thoughts with us this month on a new approach to organizing for safety. Until next time, be safe out there! - Joe Lazzara, President & CEO, Scientific Technologies Inc.
We've recognized for many years that good housekeeping is fundamental to a safe working environment. An organized workplace takes this foundation to a higher level.
What you need – where you need it – when you need it
Why should we bother with the extra effort to be organized? After all, we have computer systems and information technology to help us organize our daily lives; moreover, today's work pace is frantic, with constant change and personnel turnover. The problem is that in today's information society, we get far more information than is needed, and it often collects in our offices, files and storage rooms. A hectic pace with constant change appears to be part of everyone's future.
These are the very reasons why moving toward an organized workplace is so critical in today's fast-paced business world. Things don't get better automatically, and organization will help to reduce stress. It can also prevent "shortcuts."
When people have problems, they often take shortcuts to get a job done. Probability will eventually catch up with those who do not take time to do things the correct way. When an injury or problem occurs we typically ask why Jane or Joe didn't follow prescribed operating procedures. Factors like the stress of getting the job done, not finding the right tool, having to walk too far to do something properly or having to wait are easily overlooked causal elements. It's also common to find that the person did not know the correct way to do the task. Management often resorts to more training, warnings and use of personal protective equipment to deal with the situation.
A more enlightened approach is to organize the workplace where employees can do a job quickly and safely. Sounds good – but how to do that with the crush of deadlines and ever-increasing workload may seem insurmountable. A process proven for decades in Japanese manufacturing industry and adopted by top US companies offers a simple solution. The process is known as 5S and has five easy steps that can be applied in any environment. As you review these next few pages, think about how fundamental these steps are to establishing and maintaining planned and preventive maintenance programs. 5S is ideal for those who wish to move to the concept of "operator-owner" where a machine operator is responsible for basic maintenance.
The 5S process is comprised of five Japanese words, each beginning with "s." Their English equivalents are: Sort, Straighten, Shine, Standardize, Sustain.
What is waste?
Fundamental to successful implementation of 5S is education of the workforce to recognize the nebulous thing we call "waste." To accomplish this, we can identify problems using the following seven categories or forms of waste easily remembered as COMMWIP:
- Correction
- Over-production
- Movement of Material
- Motion (excess for people)
- Waiting
- Inventory
- Process/Procedure (lack or faulty)
Examples of waste are all around us – we just take them for granted. Once employees gain an understanding of a problem, they can begin to identify waste encountered in their daily lives.
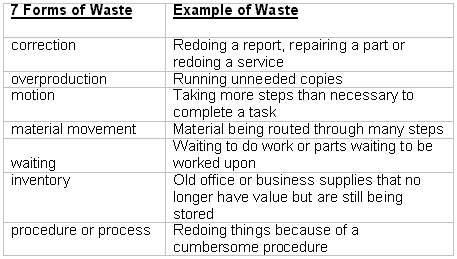
It's common to see over 50% improvement in inventory, but the application of 5S produces many benefits:
- It improves organizational efficiency.
- It reduces waste in all forms.
- It cuts hidden and direct costs.
- It cuts down employee frustration when "the system doesn't work."
- It improves speed and quality of work performance.
- It improves safety.
- It creates a visually attractive environment.
Examples of effective everyday organizers include: a silverware divider to organize your eating utensils; CD storage rack (labels make it even better); towel rack next to the sink; desk organizers for bills, letters, etc.; and tool racks.
The five steps of 5S
The five steps of 5S can be applied anytime waste is encountered, either individually or in teams. The following chart shows the repeatable 5S system.
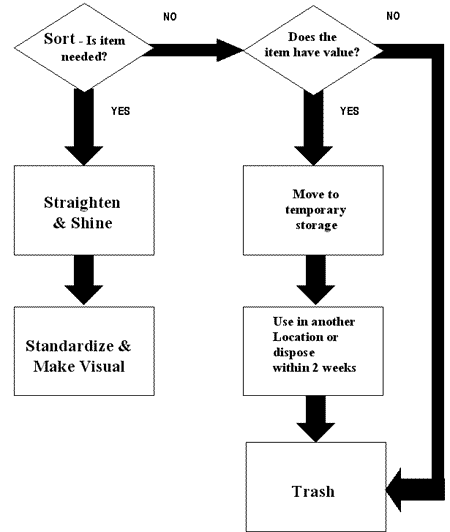
The 5S System at Work
5S is an ideal process for teamwork. Assuming you want to proceed with the effort, choose teams for specific areas. Each team (usually 3-5 people) is assigned to organize one problem area. It could be a supply cabinet, copy machine, production operation or an office. Make sure the teams take a few moments to jot down the purpose of the area. This purpose statement will be the benchmark against which the teams decide what to do with "stuff" in Step #1. (Principles are shown in bold with a >, while other key points are highlighted in bold italics.) Before you begin:
Adopt a "can-do" attitude with active top management leadership
> Allocate sufficient time for the job.
Step #1 – Sort
The first step is to sort out the things not needed in the area being organized. The trash can will usually be filled within an hour. Have a readily accessible trash receptacle with back up.
Other items create a dilemma because they may have value but are not needed in the location being organized. The fastest way to handle such items is by using red tags to identify them for transportation to a pre-determined 5S-storage area.
> "Red-tagging" is the process of putting red tags; tape or adhesive dots on items that are not needed but which might have value elsewhere. (Use common sense – if there are many small items (e.g. pencils) put them in a container that is red-tagged.)
Evaluate each item and decide whether to keep, red-tag or trash.
Get rid of anything that does not contribute to the purpose.
Red-tag anything that has value but does not meet the purpose (include questionable items).
Do you need to order items that are not currently available?
Get manager approval before a large item is disassembled.
Take red tagged items to the 5S storage area.
> Observe good safety practices - be careful when moving material (especially with others in the area).
> The more that you eliminate, the easier it will be during the next steps.
Steps #2 & #3 - Straighten and Shine
Next come the steps where you set things in order and clean them up. Your vision is to have things looking like a silverware drawer in your home, where everything is clean and easy to get because the utensils are separated.
Straighten and Shine may or may not happen concurrently. If it makes most sense to separate and straighten all items before cleaning – do so. If it seems to make sense to clean as you straighten – that's OK too.
Separate items logically and arrange them for orderly appearance. Frequently used items should be the most accessible.
Visually inspect entire area and ask:
- Why are items located where they are?
- Where should each item be?
- Have you encountered any waste - what can be done to eliminate it?
- Are tools and equipment easy to see, easy to get and easy to return?
Principles for Steps # 2 & 3 include:
> Have what you need where you need it.
> Open storage is preferred (get rid of doors whenever possible!).
> Make things visible. If you can't see what you need, you'll end up back where you began
Step #4 - Standardize and Make Visual
Visual controls are anything that help keep order in the workplace and aid employees or visitors. Signs, tape, posted procedures and directional arrows are examples of visual controls.
A visual workplace helps to reduce or eliminate many different kinds of waste in the workplace. For example, proper signs may stop numerous people from having to ask directions. Proper labels for tools, equipment and supplies may help an employee to choose the correct part during maintenance, thus reducing the risk of an injury because something could fail later. Good visual controls really help to reduce "shortcuts":
Use visible labels.
- Yellow tape should be placed on floor for items that move and may create a hazard or interference.
- Green tape may be used on walls, tables and overhead projectors (locates the overhead slide).
- Taped-off areas on walls or tables can help to group items and keep them separated.
Storage areas must be properly marked
- Use a visible colored paper for labels, instructions and standards to make them visible.
- Use pull cards or other means of visible markers to define when to reorder supplies.
A 5S Standard should include frequency of inspection to be done. Complete the standard and place it in a clear sheet protector using Velcro to mount it in a visible location. The use of visual controls is critical. Principles include:
- Provide guidance about what is expected to maintain the area properly.
- Make the Standard clear and easy to understand.
- Be sure the project area is visually clean and pleasing.
- A stranger should be able to understand what to do within 60 seconds.
- Instructions are to be posted in a visible location.
- Use labels and other appropriate visual controls.
Step #5 – Sustain
Sustain: Workshop
The first part of Sustain is what you set in place the day you complete your five steps. The second is the on-going process to maintain the improvements implemented.
Complete a 5S Maintenance Card that has room to initial for 31 days. Place it in a plastic sheet protector and use Velcro to hang it adjacent to the Standard. Use Velcro to attach a felt-tip pen.
Inspection should only take 1-2 minutes - if closed storage or lack of visual controls causes the inspection to take too much time, you may wish to make immediate improvements
The person doing the inspection (daily, weekly – whatever was decided in Step #4) must be a willing volunteer with a commitment to sustain what has been organized.
Sustain: On-Going
On-going Sustain is the most difficult step because it takes discipline.
in faithfully carrying out his/her assigned task. If something is missing or requires replacement, this person is responsible for corrective action - this will save wasted time, motion and effort on the part of someone else.
> A teammate or higher level of management should periodically check that the standard is being followed and initial
Look around at what you have accomplished. With a little effort, the area will be maintained just as it looks right now. Keep applying 5S and you'll find that an entire department or plant can actually get organized and stay that way. Less stress, less risk and productivity improvements, 5S can help to make your workplace better.
About the author: Michael Taubitz graduated from General Motors Institute with a Mechanical Engineering degree in 1970 and from Central Michigan University with a Masters Degree in 1980. He started his career at the Chevrolet Flint Engine Plant in 1965. Following a number of plant and divisional assignments in Personnel and Engineering, he was appointed Manager of Occupational Safety and Health for the Chevrolet - Pontiac - Canada Group in 1984. In 1986, he became the Corporate Director of Safety and Ergonomics for General Motors worldwide. Mr. Taubitz assumed the position of Co-Director of the UAW-GM Center for Health and Safety in 1993, and later moved to engineering to establish a new Design-In Safety Center in 1995. In 1997, he became a Manager of Industrial Engineering for GM North American Operations, overseeing a number of engineering functions. In 1999, he established GM's new activity to provide technical liaison for emerging global health and safety issues. (Back)