Reducing Workplace Risks with Chemical Protective Clothing
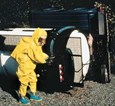
By James P. Zeigler, Ph.D.
Spurred by the Occupational Safety and Health Act of 1970, the drive to protect workers from hazards in the workplace is becoming a top priority for businesses throughout the U.S. Among these hazards are the wide variety of chemicals which pose a risk to workers involved in manufacturing today's consumer and industrial products.
Safety experts at plants that use industrial chemicals must prepare for a wide range of potential exposure scenarios involving handling, transporting and using these diverse and sometimes hazardous chemical compounds. Whether it's a leaky drum in a storage warehouse, a ruptured process line, or an overturned tanker on a public highway, a chemical exposure hazard must be handled with the utmost care and concern for worker safety.
In all cases, industrial hygiene experts (and OSHA) agree that the preferred way to protect employees from workplace hazards is to remove the hazards through process changes, engineering controls, or administrative procedures. Where these steps are not sufficient to ensure worker safety, the use of personal protective equipment—including chemical protective clothing—is recommended.
Analyzing the Need for Chemical Protective Clothing
Before selecting protective clothing, perform a hazard assessment to determine the exact nature of the risk and the degree of protection required. There are many types of industrial chemicals and they differ widely in their toxic and corrosive effects. Conduct an analysis of the chemical exposure conditions at the specific work site to determine the type of fabrics and materials required for the protective garments that should be worn at that site.
Applicable regulations and standards also play an important role in the selection and use of chemical protective clothing. Consult these regulations when selecting garments. There are mandatory standards that must be met by industrial protective clothing, including OSHA's PPE regulations in 29CFR 1910.132-136. These standards are readily accessible on the Internet at http://www.osha.gov.
There are also voluntary consensus standards that are only suggested guidelines. Examples of consensus standards are the protective equipment standards and practices issued by industry and trade groups such as the National Fire Protection Association (NFPA), the American Conference of Governmental Industrial Hygienists (ACGIH) and the American Society for Testing and Materials (ASTM).
OSHA's general PPE regulations contain individual sections that list requirements for eye, face and head protection in chemical environments. For protection against hazardous chemicals, OSHA 1910.130 (Hazardous Waste Operations and Emergency Response - HAZWOPER) lists special requirements for protective ensembles that cover garments as well as breathing apparatus. EPA's Agricultural Workers Standard and OSHA's Lead and Asbestos Standards also contain specific sections on personal protective equipment.
Evaluating Different Types of Chemical Protective Clothing
Resistance to chemicals and physical durability are critical elements in the proper performance of protective clothing selected for chemical exposure. There are three ways that chemicals can affect the material used in a protective garment: degradation, penetration, and permeation.
Degradation is a physical change in the material caused by contact with the chemical; penetration refers to the passage of the chemical through openings in the material; and permeation is the movement of the chemical through the material at a molecular level.
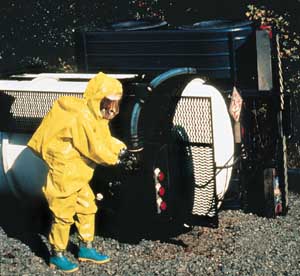
No single garment fabric can provide resistance to all chemicals under all conditions, so it is important to test against the specific conditions of the workplace to determine if a garment possesses the resistance to degradation, penetration and permeation required for adequate protection. OSHA has adopted the Environmental Protection Agency's (EPA) guidelines, which define four distinct levels of protection against hazardous material that can be provided by chemical protective clothing:
Level A protective clothing is worn when the highest level of skin, respiratory and eye protection is required. Generally, this consists of a totally encapsulating, chemical protective ensemble worn with a positive-pressure, self-contained breathing apparatus (SCBA) and inner and outer chemical-resistant gloves and steel-toe boots.
Level B protective clothing is worn when the highest level of respiratory protection is required, but a lesser degree of skin protection is needed. This usually consists of a hooded, splash-resistant protective suit worn with an SCBA, and inner and outer chemical resistant gloves, steel-toe boots and hard hat.
Level C protective clothing provides a lower level of respiratory protection and is worn when the criteria for using air-purifying respirators are met. Level C equipment includes an approved air-purifying respirator and chemical splash-resistant clothing, and inner and outer chemical-resistant gloves and steel-toe boots.
Level D protective clothing is basically a standard work uniform and provides minimal protection against nuisance contamination only. This generally consists of coveralls and chemical-resistant, steel-toe boots.
Proper Use and Care of Chemical Protective Clothing
Once the protective ensemble has been selected, employees must learn how to don and doff the equipment, enter a potentially dangerous environment, and perform an assigned task. Afterwards, they must remove the clothing without contaminating themselves or others and either dispose of the garments or clean and store them for future use.
Misuse of chemical protective clothing could result in injury or even death. For this reason, workers and their employers must be able to recognize potential malfunctions and learn how to decontaminate and dispose of garments in a safe, environmentally sound manner. A hands-on training program is the best way to achieve familiarity with proper procedures.
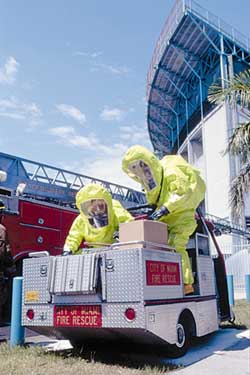
OSHA's PPE regulations require that chemical protective clothing and equipment be inspected, cleaned and repaired at regular intervals to maintain the required level of chemical protection. This standard also requires that ensembles that cannot be decontaminated be retired and disposed of in a manner that protects employees from exposure hazards.
Worker Comfort: The Issue of Heat Stress
A comfort factor known as heat stress must be considered when selecting and wearing chemical protective clothing for an extended period of time. Heat stress is the strain placed on the body as it attempts to cope with the excess internal heat caused by barrier protective garments. Since the effects of heat stress can prove fatal if not properly controlled, it is important to monitor the comfort level of workers wearing chemical protective clothing.
Aside from its physical effects on the worker, heat stress also increases the potential for accidents. Employees subjected to excessive heat may be distracted and experience loss of motor skills. Fainting is common; in extreme cases, heat stress can lead to permanent injury or death. Workers exposed to high temperatures, humidity and/or radiant heat should be trained to recognize and deal with the problems related to heat stress.
Personal protective equipment designed to reduce heat stress includes heat-reflective clothing and special-purpose garments cooled with ice, gels, cold water or air-circulation systems. However, in hot, potentially stressful situations, workers must be alerted to the signs and symptoms of heat stress and be able to regulate their activities to avoid the problem. They should be reminded that heat stress potential cannot be solved by simply changing clothes.
BIO: James P. Zeigler, Ph.D., is research manager for DuPont Tyvek Protective Apparel. He holds a patent on chemical protective clothing fabrics and has written a host of technical papers and articles for a variety of industry publications. Zeigler has particular expertise in protective apparel fabric technology, protective apparel industry regulations and standards, and weapons of mass destruction. DuPont Protective Apparel, a business inspired by the company's leadership in chemicals and in fabrics for protection against heat, flame, puncture and projectiles, offers a broad selection of limited-use and reusable chemical-resistant garments for workers in industrial environments. This premier line of protective apparel includes: Tychem chemical protective clothing, DuPont StaSafe Garments, and Tyvek ProtectiveWear. For more information, please visit the DuPont Protective Apparel Website: http://www.dupont.com/tyvek/protective-apparel, or call DuPont toll-free at: 1-800-44-TYVEK.
Note: The information contained in this feature is based on technical data that DuPont believes to be reliable. This information is subject to revision as additional knowledge and experience are gained. DuPont makes no warranties, express or implied, including without limitation, no warranties of merchantability or fitness for a particular use. DuPont assumes no obligation or liability whatsoever in connection with any use of the information contained in this article. This information is not intended as a license to operate under or a recommendation to infringe any patent or technical information of DuPont or others covering any material or its use.