ISO 9000:2000: New Standard for Excellence
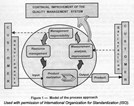
By James B. Elliott, PE, CQE
The ISO 9000 international quality management systems standard has undergone a major overhaul. Learn what it's all about, and how it may affect you.
Contents
Background
Timeline
What's Different?
Conversion to the New Standards
Summary
You are probably, by now, more or less familiar with ISO 9000, and you've probably heard talk about the new revision known as ISO 9000:2000. If so, you may have some questions and concerns. This article will cover the high points of the new standard, so that you can become familiar with its content and the potential implications for you and your company.
Background (Return to Contents)
The International Organization for Standardization (ISO) is a non-profit organization established to enhance international cooperation and commerce by coordinating the development and dissemination of standards for uniform business practices. It is supported by the sales of published standards, as well as the active participation of its member nations, representing virtually the entire economically developed world. ISO standards are developed by committees consisting of experts in the subject field from around the world and are also ratified by a vote of the member nations.
First adopted and issued in 1987, ISO 9000 is a series of standards for requirements in quality management systems. The purpose is to level the playing field for the management of quality for the world's commercial products and services so that all nations will have a common basis for acceptance of each other's goods in free trade.
It is ISO policy to review and update each issued ISO standard approximately every 5 years. The purpose is to ensure that the standards are maintained consistent with the contemporary state of the art and proven implementations of the field of business practice involved.
The standard underwent a relatively minor, primarily clarifying, update in 1994. However, the 2000 update is a major structural and strategic revision of the 9000 series of standards. It incorporates several concepts that will tend to bring the standard into better alignment with what are widely considered to be "best practice" strategies for contemporary quality management systems.
The old ISO 9002 and 9003 standards will become obsolete with the issue of ISO 9000:2000.
The familiar 20 elements that form the structure of the current ISO 9000:1994 series standards will be folded into a new structure with four main chapters:
- management responsibility
- resource management
- product and/or service realization
- measurement, analysis, and improvement
These four chapter topics describe the four phases of a fundamental concept of the new standards referred to as the Process Model. (Editor's Note: For a comparison of the revisions and the ISO 9000:1994 standards, click here.)

Many users of the current ISO 9000 series of standards find them to be disjointed and confusing. One of the specific goals of the 2000 revision committee has been to maintain structural consistency and harmony of content in the new standards. Both of the new documents will be organized to have the same organizational structure and sequence, based on the above four-phase process model.
These two documents now form what ISO calls a "consistent pair" of quality management standards. It's intended that the 9001 document will define the minimum requirements and that 9004 will provide guidance for companies to go beyond the minimum requirements by a process of Continual Improvement.
This concept of continual improvement is one of the additions to the old standard's requirements. The old Customer Complaint, Self-Audit, and Corrective and Preventive Action requirements were pointed in the direction of continual improvement, but now it will be a fundamental theme.
Another fundamental difference in the new standards' requirements is the extension of customer awareness and concern beyond a customer complaint system (4.14.3) to the requirement for actual measurement of customer satisfaction. The concept of customer satisfaction as a metric for quality system performance is a scoring criterion for the U.S. Commerce Department's coveted Malcolm Baldrige National Quality Award for excellence in quality management and a standard feature of most modern quality management philosophies and paradigms.
The third major new requirement emphasis is in the area of Resources. The 1994 standard contains a single paragraph (4.1.2.2) that refers to the requirement for management to provide necessary resources to support the Quality System. The new standard will place more emphasis on the need to provide and make available specific types of resources. The required resources will include such elements as information, communication, infrastructure, and work environment protection.
Many will be pleased to hear that the new standards have also been designed to be better aligned and compatible with ISO 14001. In fact, there is a good chance that with the next revision of these two standards systems, they will become one.
Conversion to the New Standards (Return to Contents)
If your company is currently certified to one of the existing ISO 9000 standards, you may be wondering if it was a waste of time and money. This might cause particular concern if the existing certification is to the soon-to-be obsolete 9002 or 9003 standard.
The good news is that the new consistent pair of standards is designed to stand on the shoulders of the old system. So, if you now have ISO 9000:1994 certification, you already have the foundation in place to make the transition to the new 2000 standard. The details for how this can be best accomplished will, of course, be different for each case.
NOTE: If you haven't done so, you should arrange discussions with your ISO 9000 registrar (the organization that issued your certification) as soon as possible to plan an orderly transition based on your particular situation.
As you probably found during your original certification program, registrars are not allowed to counsel you regarding the details for "how" to design your quality system, only "what" features it must have to be conforming. You will again likely need the services of a quality management systems consultant to implement a smooth transition.
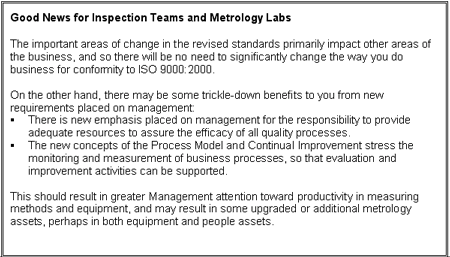
Although there will most likely be a need for some new policies and procedures, and the quality policy manual will need to be reorganized, most of your existing documentation will simply fold into your new ISO 9000:2000 quality management system.
There is a planned two-year transition period after the adoption of the revised standard, during which quality management systems conforming with either the 1994 revision or the 2000 revision will be accepted. However, because most registrars' existing certification contracts are based on a three-year reassessment schedule, you and your registrar may find it most cost-effective to adjust your plan for certification changeover to coincide with the next scheduled re-certification assessment. Many registrars are encouraging phased transitions, correlated with their six-month surveillance audit schedules.
If you're involved in the certification process at your employer, this is another reason not to put the issue off, but to meet with your registrar's business representative as soon as possible to work out the best transition plan for your situation.
Summary (Return to Contents)
The pending major revision of ISO 9000 standards is a necessary "raising of the bar" to take the standards to the next level of excellence. The new standards will build on the old requirements, with the goal of causing continual improvement of quality performance, resulting in continually enhanced customer satisfaction.
No organization that's now certified to an ISO 9000:1994 standard should feel anxious about being able to transition to the revised standard. By already being certified under the 1994 standard and at the same time adapting to the new requirements, one can implement a suitable plan for worry-free transition on the best timeline for your situation. Done right, you should hardly notice the transition taking place.
If you are planning to achieve ISO 9000 certification for the first time, the good news is that the new standards provide more flexibility for conformity. As a result, you should find certification more easily attainable than may have been possible under the old standards. In addition, service industry organizations will find the new standards much more easily applied to your business processes.
In any case, your registrar and consultant can both provide advance planning tips, to assure your smooth transition into conformity with ISO 9000:2000. But to do so, it is important to start the process now.
Sources:
- ISO/DIS 9000:2000, ISO/DIS 9001:2000, and ISO/DIS 9004:2000, November 1999
- ISO 9001:1994, Quality Systems - Model for Quality Assurance in Design, Development, Production, Installation, and Servicing
- ISO/TC 176/SC 2/N 439, (Draft) Transition Planning and Guidance, May 1999
- ISO Bulletin, Summary of the Year 2000 Revision of ISO 9000 Quality Management System Standards, May 1999
About the Author
Editor's Note: For related information, visit the ISO website (http://www.iso.ch/).
James B. Elliott is a management consultant in Southern California specializing in quality management systems. He has more than 25 years of experience in medical, automotive, aerospace, and consumer product R&D and operations management. For the last eight years, Elliott has been assisting companies to achieve ISO certification for their quality management systems and the CE Mark for their products. The reader is invited to visit his website at http://www.1stNclass.com.
Section No. |
ISO DIS 9001:2000 Section Heading |
Corresponding ISO 9001:1994 Sections |
5 |
Management responsibility |
|
5.1 |
Management commitment |
4.1; 4.1.2.2; 4.2.1 |
5.2 |
Customer focus (new) |
|
5.3 |
Quality policy |
4.1.1 |
5.4 |
Planning: |
----- |
5.4.1 |
Quality objectives |
4.1.1; 4.2.1 |
5.4.2 |
Quality planning |
4.2.3 |
5.5 |
Administration: |
----- |
5.5.1 |
General |
----- |
5.5.2 |
Responsibility and authority |
4.1.2 |
5.5.3 |
Management representative |
4.1.2.3 |
5.5.4 |
Internal communication (new) |
|
5.5.5 |
Quality Manual |
4.2.1 |
5.5.6 |
Control of documents |
4.5 |
5.5.7 |
Control of quality records |
4.16 |
5.6 |
Management review: |
4.1.3 |
5.6.1 |
Review input |
4.1.3 |
5.6.2 |
Review output |
4.1.3 |
6 |
Resource management |
|
6.1 |
Provision of resources |
4.1.2.2 |
6.2 |
Human resources: |
----- |
6.2.1 |
Assignment of personnel |
4.1.2.1 |
6.2.2 |
Training, awareness and competency |
4.18 |
6.3 |
Facilities |
4.9 |
6.4 |
Work environment |
4.9 |
7 |
Product realization |
|
7.1 |
Planning of realization processes |
4.2.3; 4.9; 4.10; 4.15; 4.19 |
7.2 |
Customer-related processes: |
----- |
7.2.1 |
Identification of customer requirements (new) |
|
7.2.2 |
Review of product requirements |
4.3 |
7.2.3 |
Customer communication (new) |
|
7.3 |
Design and/or development: |
4.4 |
7.3.1 |
Design and/or development planning |
4.4.2; 4.4.3 |
7.3.2 |
Design and/or development inputs |
4.4.4 |
7.3.3 |
Design and/or development outputs |
4.4.5 |
7.3.4 |
Design and/or development review |
4.4.6 |
7.3.5 |
Design and/or development verification |
4.4.7 |
7.3.6 |
Design and/or development validation |
4.4.8 |
7.3.7 |
Control of design and/or development changes |
4.4.9 |
7.4 |
Purchasing: |
----- |
7.4.1 |
Purchasing control |
4.6 |
7.4.2 |
Purchasing information |
4.6 |
7.4.3 |
Verification of purchased products |
4.6 |
7.5 |
Production and service operations: |
----- |
7.5.1 |
Operations control |
4.9; 4.10; 4.12; 4.19 |
7.5.2 |
Identification and traceability |
4.8 |
7.5.3 |
Customer property |
4.7 |
7.5.4 |
Preservation of product |
4.15 |
7.5.5 |
Validation of processes |
4.9 |
7.6 |
Control of measuring and monitoring devices |
4.11 |
8 |
[System] Measurement, analysis and improvement |
|
8.1 |
Planning |
4.10; 4.20 |
8.2 |
Measurement and monitoring: |
----- |
8.2.1 |
Customer satisfaction (new) |
|
8.2.2 |
Internal audit |
4.17 |
8.2.3 |
Measurement and monitoring of processes |
4.20 |
8.2.4 |
Measurement and monitoring of product |
4.10; 4.20 |
8.3 |
Control of nonconformity |
4.13 |
8.4 |
Analysis of data |
4.14; 4.20 |
8.5 |
Improvement: |
----- |
8.5.1 |
Planning for continual improvement |
4.1.3; 4.9 |
8.5.2 |
Corrective action |
4.14 |
8.5.3 |
Preventive action |
4.14 |
This reference chart is based on the ISO Draft International Standard 9001:2000 prepared by ISO Technical Committee 176 for approval by the ISO members. Final approval and issue as a standard is planned by the end of year 2000.
The chart was prepared for general reference. Users should adhere to the detailed requirements of the applicable final issued ISO Standards to establish quality management systems conforming to the ISO 9000:2000, 9001:2000 and 9004:2000 standards.
Copies of the MS Word* file, updated as appropriate, are available free on the www.1stNclass.com website.
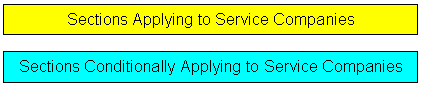
Section No. |
ISO DIS 9001:2000 Section Heading
Corresponding
ISO 9001:1994 Sections
5
Management responsibility
5.1
Management commitment
4.1; 4.1.2.2; 4.2.1
5.2
Customer focus (new)
5.3
Quality policy
4.1.1
5.4
Planning:
-----
5.4.1
Quality objectives
4.1.1; 4.2.1
5.4.2
Quality planning
4.2.3
5.5
Administration:
-----
5.5.1
General
-----
5.5.2
Responsibility and authority
4.1.2
5.5.3
Management representative
4.1.2.3
5.5.4
Internal communication (new)
5.5.5
Quality Manual
4.2.1
5.5.6
Control of documents
4.5
5.5.7
Control of quality records
4.16
5.6
Management review:
4.1.3
5.6.1
Review input
4.1.3
5.6.2
Review output
4.1.3
6
Resource management
6.1
Provision of resources
4.1.2.2
6.2
Human resources:
-----
6.2.1
Assignment of personnel
4.1.2.1
6.2.2
Training, awareness and competency
4.18
6.3
Facilities
4.9
6.4
Work environment
4.9
7
Product realization
7.1
Planning of realization processes
4.2.3; 4.9; 4.10; 4.15; 4.19
7.2
Customer-related processes:
-----
7.2.1
Identification of customer requirements (new)
7.2.2
Review of product requirements
4.3
7.2.3
Customer communication (new)
7.3
Design and/or development:
4.4
7.3.1
Design and/or development planning
4.4.2; 4.4.3
7.3.2
Design and/or development inputs
4.4.4
7.3.3
Design and/or development outputs
4.4.5
7.3.4
Design and/or development review
4.4.6
7.3.5
Design and/or development verification
4.4.7
7.3.6
Design and/or development validation
4.4.8
7.3.7
Control of design and/or development changes
4.4.9
7.4
Purchasing:
-----
7.4.1
Purchasing control
4.6
7.4.2
Purchasing information
4.6
7.4.3
Verification of purchased products
4.6
7.5
Production and service operations:
-----
7.5.1
Operations control
4.9; 4.10; 4.12; 4.19
7.5.2
Identification and traceability
4.8
7.5.3
Customer property
4.7
7.5.4
Preservation of product
4.15
7.5.5
Validation of processes
4.9
7.6
Control of measuring and monitoring devices
4.11
8
[System] Measurement, analysis and improvement
8.1
Planning
4.10; 4.20
8.2
Measurement and monitoring:
-----
8.2.1
Customer satisfaction (new)
8.2.2
Internal audit
4.17
8.2.3
Measurement and monitoring of processes
4.20
8.2.4
Measurement and monitoring of product
4.10; 4.20
8.3
Control of nonconformity
4.13
8.4
Analysis of data
4.14; 4.20
8.5
Improvement:
-----
8.5.1
Planning for continual improvement
4.1.3; 4.9
8.5.2
Corrective action
4.14
8.5.3
Preventive action
4.14
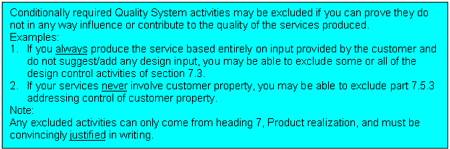
This reference chart is based on the ISO Draft International Standard 9001:2000 prepared by ISO Technical Committee 176 for approval by the ISO members. Final approval and issue as a standard is planned by the end of year 2000.
The chart was prepared for general reference. Users should adhere to the detailed requirements of the applicable final issued ISO Standards to establish quality management systems conforming to the ISO 9000:2000, 9001:2000 and 9004:2000 standards.
Copies of the MS Word* file, updated as appropriate, are available free on the www.1stNclass.com website.