LAB SAFETY REVIEW: "Gowning-Up" for Cleanroom Safety
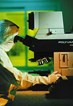
Written by Peter D. Gabele, DuPont Tyvek Protective Apparel
Lab Safety Review is a new monthly column on Safety Online and Laboratory Network.com. Each edition is written by a specialist in this important field. This is the second installment of the January column.
Pay a visit to a modern-day manufacturing plant and you could be in for a big surprise. What you find may look more like a clinical laboratory than the stereotype production line, with its chattering equipment and steaming processes. That's because ultra-cleanliness has become a critical requirement in many of today's high-tech industries where the focus is on miniaturization, fine detail, and functional precision.
Hyper-pure manufacturing environments have become standard in much of the aerospace, electronics, and medical industries, where even the hint of contamination can be intolerable. This surging demand for operational cleanliness has given birth to a new manufacturing discipline known as "cleanroom" or "clean-area" technology—a discipline often characterized by the encapsulated suits or "bunny suits" worn by workers to protect both themselves and the sensitive products that they make.
Worker Apparel Serves as Two-Way Protection
Contamination of products during the manufacturing process can be traced to several causes, including the production workers themselves. Three common forms of employee-generated contamination are skin flakes, particles from street clothing, and cosmetic products. To prevent the transfer of these and other foreign materials onto the product being made, employees who work in clean area environments often wear fully encapsulated suits.
However, cleanroom garments also serve a second important function. They act as protective apparel to safeguard workers from exposure to the hazardous chemicals and particulates found in many high-tech manufacturing processes.
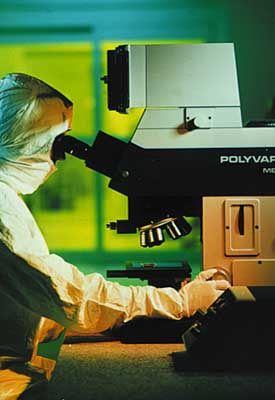
In the semiconductor industry, for example, many of the chemicals and compounds used to etch, polish, and clean semiconductors are so aggressive that workers must wear protective apparel to prevent skin contact with these hazardous materials. To be effective, cleanroom garments must be made from materials that not only prevent the passage of worker-generated contaminants into the workplace, but also prevent entry of hazardous materials that may endanger the health or safety of the employee.
Performance Requirements and Fabric of Cleanroom Apparel
Cleanroom garments require key performance characteristics that differ from other types of protective clothing. These performance characteristics include:
- Particulate Barrier - Garments should be effective in barring the passage of dry particulate matter in either direction through the fabric.
- Microbial Contamination - Garments should hold out the passage of microorganisms.
- Chemically and Biologically Inert - Garments should resist liquid absorption and should protect the worker against a wide range of chemicals, solvents and biohazards.
- Non-contaminating - Garments should not shed fiber particles or flakes or generate other matter that will contaminate the product.
- Strength and Durability - Garments should be highly resistant to abrasion, puncture, and tearing.
- Light Weight - Garments should be thin, "drapeable," and comfortable for the wearer.
- Sterilization - Garments should be able to be sterilized by conventional steam and gamma radiation methods.
- Reprocessability - Single-use garments should be able to be reprocessed to reduce disposal costs.
- Breathability – Cleanroom garment thermal comfort is governed by the flow of warm humid air way from the body. Static vapor diffusion, described as MVTR (moisture vapor transmission rate), can be a misleading indication of thermal comfort in high-barrier garments. According to recent DuPont-sponsored research, garment thermal comfort is explained by airflow through the garment fabric that occurs during normal body movements, even with high-barrier, porous materials such as Tyvek.
- Electrostatic Properties - Garments should not create build-up of static electricity while being worn.
- Laundering - Garments should resist deterioration and loss of properties from normal washing and dry cleaning processes.
This demanding list of performance requirements has led to the development of special fabrics for use in cleanroom garments. Designed to provide protection for both worker and product, these high-performance fabrics include woven polyester (herringbone or taffeta), DuPont Tyvek spunbonded polyolefin, Gore-Tex expanded PTFE laminate and other fabrics. These materials provide different levels of barrier protection and are resistant to different combinations of hazardous materials. Selection of the proper fabric and garment design is based on the class of cleanroom involved as well workplace conditions in the area of use.
Garments made from woven polyesters are commonly used in Class 100 through Class 100,000 electronic cleanrooms. These fabrics exhibit good electrostatic and MVTR properties. Frequent laundering, however, can create "contamination windows" that result in decreased particle filtration efficiency. Woven fabrics usually offer poor barrier protection against microbiological organisms and liquid chemicals.
Gore-Tex, which is a woven polyester knit with a thin, adhesive-bonded outer layer of expanded PTFE, is suitable for Class 1 to Class 10 electronic cleanrooms. The fabric is recognized as having one of the highest MVTR properties, and provides efficient filtration of dry particulates of 0.1 micron and larger. While Gore-Tex garments can be reused repeatedly, the fabric requires special laundering. Abrasion, stretching, and flaking are the major performance concerns with extended use of this fabric.
Tyvek spunbonded polyolefin is a high-density polyethylene sheet structure manufactured by DuPont for Class 100 to Class 1,000 cleanrooms. In addition to good MVTR properties, it offers higher air porosity than microporous films, yet maintains excellent filtration efficiency (down to 0.5 microns). Tyvek also provides a barrier to microorganisms. The material is 60% lighter than woven polyester, and its strength and durability guard against flaking and breaking of fibers that might lead to product contamination. Tyvek can be gamma-, ETO-, or steam-sterilized and is easily laundered.
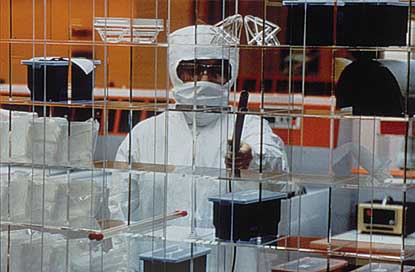
The Importance of Workplace Behavior: "Gowning-Up" and "Gowning-Down"
Proper donning and doffing of apparel is a critical part of the overall cleanroom garment system. The most sophisticated, high-tech cleanroom garments will never meet their designed performance levels unless employees follow specific guidelines for proper use.
It is critical to develop general donning and doffing guidelines to meet contamination control requirements of the clean area, as well as to accommodate the design layout of gown rooms and the needs and concerns of the wearers. When developing gowning SOPs (standard operating procedures), give top priority to employee training and qualification. Documented training of new employees, coupled with periodic retraining and enforcement of regulations, will help maintain good cleanroom practices and discipline.
To maintain efficient cleanroom operations, employers should prescreen employees for certain physiological characteristics that might result in contamination of the environment or disruption of the manufacturing process. These include possible allergies to synthetic fibers and solvents; respiratory and skin diseases; severe nervous or mental conditions; and other employee traits that can affect performance of the work team. Personal hygiene of workers is equally important. Employees should bathe and shampoo hair frequently, shave daily and keep hair neat and trim.
In addition, site-specific employee restrictions and workstation practices, such as proper object transportation and housekeeping requirements, should be observed by all employees involved in clean area operations.
About the author: Peter D. Gabele is the cleanroom/controlled environments manager for DuPont Tyvek Protective Apparel. He is responsible for the development of new products, sales and marketing of apparel made of Tyvek and Tychem, primarily for the electronic, biotech, and pharmaceutical markets in the U.S. and Puerto Rico. Gabele can be contacted by phone at 281-381-6419 or by e-mail at peter.d.gabele@usa.dupont.com.
For more information about protective apparel for cleanroom applications, contact DuPont Tyvek Product Information at 1-800-44-Tyvek or visit the Tyvek home page on the Internet at www.dupont.com/tyvek/protective/apparel.
Tyvek is a DuPont registered trademark.
Note: This information is based on technical data that DuPont believes to be reliable. This information is subject to revision as additional knowledge and experience are gained. DuPont makes no warranties, express or implied, including without limitation, no warranties of merchantability or fitness for a particular use. DuPont assumes no obligation or liability whatsoever in connection with any use of the information contained in this article. This information is not intended as a license to operate under or a recommendation to infringe any patent or technical information of DuPont or others covering any material or its use.