Practical Applications for Work Zone Safety
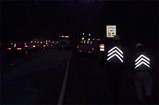
Work zone safety is a fairly complex mix of elements, and to a large extent can be effectively addressed by using a combination of traditional and non-traditional construction safety methods. This article reviews alternate strategies and suggests innovations and refinements to help manage this important exposure. The focus is on interstate highway work zones.
Who's at Risk?
Safety Vests are Key to Worker Protection
OSHA Requirements
Subcontractor Safety is Important
Traffic Control and Signage
Most construction activity will, at one time or another, involve exposure to vehicular traffic. According to a recently released report by the Bureau of Labor Statistics, highway crashes are at the highest level in the past seven years. From an occupational standpoint, we're more at risk of death or injury while driving to and from work than we are AT work!
For those employees and operations not routinely familiar with traffic control safety practices, additional precautions and advance planning are strongly advised, and in many cases required, for full job safety compliance.
Getting the job done safely is everyone's goal. While your employees may be accomplished craft persons or technicians, they may have only a limited understanding and awareness of standard traffic safety measures. In some cases, it might be wise to call in a professional to assist with traffic safety.
Who's At Risk? (Back to Top)
There are two separate populations primarily "at risk" in highway work zones: employees and motorists.
Safety controls for protecting each population are fairly distinct, and depend upon separate regulatory definitions and applications. Employee safety is largely governed by Occupational Safety & Health Act (OSHA) requirements, while motorist protections derive from U.Ss and state Department of Transportation sources, primarily the Manual for Uniform Traffic Control Devices (MUCTD).
A thorough knowledge of each set of regulations is important to select and implement the best combined protection for your work zone. Elements of DOT and OSHA must be blended to provide the highest level of safety. Basic applied risk management practices instruct us to eliminate, avoid, reduce, or control the exposures to risk of each population. Achieving this protection in high-speed traffic environments requires engineering, planning, enforcement, and close supervision.
Safety Vests are Key to Worker Protection (Back to Top)
One of the most important safety "tools" for employees in the work zone is the safety vest. The importance of this article of clothing cannot be overstated. The safety industry has long recognized this, and recently the American National Standard Institute ( ANSI) adopted a standard addressing safety vest performance characteristics. ( ANSI/ISEA 107-1999) . Vests and apparel are classified by conspicuity type, according to their highway environment. Basically, the standard says that the faster the traffic, the brighter the vest.
Interstate highways require the most conspicuous apparel available. All persons in the work zone should wear safety vests at all times when on the right of way (ROW). This includes work behind Jersey barriers, guard rails, on medians, etc. Vests must be high-visibility orange or lime green and have contrasting and reflective striping for incidental night visibility.
Night work jobs should consider using 100% reflective vests, which are more costly (approximately $40 per vest versus $23 for traditional vests). The difference in worker visibility and appearance is appreciable (see photo inset).

In some cases, high visibility apparel, such as coveralls, jacket and pants combinations, may also be used. Some vest manufacturers offer ‘nape protectors' in high visibility colors and striping. These units attach to hard hats and protect from direct sunlight exposure, and also add square inches of high visibility surface area to the visual field of approaching motorists.
OSHA Requirements (Back to Top)
OSHA requires that workplaces be assessed for personal protective equipment (PPE) needs. In addition to safety vests, which have been defined by OSHA as PPE, gear should include:
- Approved hard hats, preferably in lighter colors to improve visibility. Use of low tension, break-away chin straps and adjustable headgear is recommended to keep hats in place during high wind turbulence, such as proximity to 18-wheelers blowing by. In addition to preventing head injuries, bright colored helmets are supplemental identification devices- particularly when fluorescent or reflective decals are applied.
- Helmet liners are also advised. A good quality liner is surprisingly comfortable in most weather conditions. Be sure they have break-away chin straps.
- Good footwear, either boots or shoes, appropriate to job conditions and requirements. Safe and solid footing is essential in any occupational setting, and it is doubly important around high-speed interstates.
- Additional PPE, such as eye protection, should be selected and matched to the needs of the job. For example, goggles are more effective than spectacle-type glasses at preventing eye injuries from dust, flying particles, and chemical splash. The safety equipment industry has recently engineered several innovative, low-profile, goggle designs that are worth trying in a lot of applications. Make certain all gear is ANSI-approved.
Other OSHA safety requirements may involve fall protection, confined space safety, trench and excavation safety, overhead lines clearance, underground utility identification and protection, back up alarms on heavy equipment, lockout/tagout, and electrical safety. Pre-work meetings should address unusual hazards and agree on ways to control them.
Subcontractor Safety is Important (Back to Top)
The highway authority or general contractor should ensure that sub-contractors have a good safety program in place to addresses anticipated and potential exposures. Specific safety rules may be posted on the job site, to eliminate the time honored excuse of "No one told ME about that rule." This is especially troublesome in view of the high labor turnover rates among construction trades, including crew supervisors. Bilingual safety signs may also be advisable.
An indicator of a sub-contractors relative safety performance may be found by examining their workers' compensation experience modification factor or EMF. Reviewing this numerical rating can offer an insight as to how a contractor's safety record stacks up against similar companies in their industry.
An EMF of 1.0 means they are "average". Below 1.0 means they are "better than average" by the percentage represented by the placement of the decimal point. An employer with a .90 EMF, for example, has a 10% better than average injury and illness rate as represented by its workers' compensation experience. An EMF above 1.0 means a company is "worse" than average, which should cause you to ask more in-depth questions about its safety program and plan to inspect job site safety conditions more closely.
Remember: It's always appropriate and instructive to ask for evidence of a sub-contractor's safety program, such as a copy of their safety manual or other documentation. Other questions to ask at pre-work meetings with subcontractors include:
- How often are job site safety meetings held?
- Are meeting topics relevant to the job, and do they include traffic safety reminders and requirements?
- Are site supervisors adequately versed in applicable safety requirements?
By learning everything that you can about the subcontractors' safety programs, policies and attitudes before work starts, you can prevent a number of hazardous situations from ever developing.
Contract language tips: Contracts made with subcontractors should be carefully worded with specific safety and directive language, as opposed to general clauses such as "…agrees to comply with all safety regulations…" If you are referencing OSHA, then say OSHA, and provide a specific standard number. If you reference state or U.S. DOT regulations, provide a specific reference. If your company has specific safety rules which go beyond what OSHA or DOT require, they should be clearly stated and discussed in advance to avoid misinterpretation in the field.
Traffic Control and Signage (Back to Top)
Special attention should be devoted to traffic control device (TCD) placement—detail it on the project traffic safety plan—and also to maintenance and frequent inspection of all TCD's. This responsibility often becomes diffused once the job begins. Most sub-contractors are very good in their chosen field of expertise, paving, digging, building, etc., but will gradually relegate checking signs and TCD's to a secondary status. In fact, maintaining TCD placement and signage is an extremely important responsibility.
TCD's must be erected properly and frequently inspected during the work shift, to ensure they remain properly placed. A log entry, checklist or other type of documentation should be used to verify that the inspections were made, and any corrective actions noted. The frequency of TCD inspections should be matched to job site conditions. For example, temporary, flexible stand advance warning signs on interstates are subject to displacement by turbulence from semi trailers. A pair of binoculars in a central vantage point may help, but driving through the work zone is recommended at frequent intervals.
Exactly who will be responsible for inspecting TCD's should be clearly stated and recorded at the pre-work meeting. Responsibility and accountability for safety performance is best achieved when a person knows it is his or her job, and that someone will periodically audit the TCD records. In the highly litigious climate surrounding accidents, records proving TCD's were erected and maintained are very helpful to refute the inevitable allegation of negligence.
A word about signage: reflective panel signs should be closely inspected to make certain they are in optimum condition. A motorist has less than 15 seconds to see, recognize, read, and react to the directions on a 48" x 48" reflective panel at night on an interstate. Deduct from this time allotment for rain or other inclement weather. Never take a chance with dirty, damaged, or smudged signs or devices.
Reflective panel signage relies on vehicle headlamps for illumination. Considering that a healthy percentage of vehicles have improperly adjusted, dirty, weak, or otherwise less than optimal headlamps, sign clarity can make a big difference. The development of programmable message signs and arrow boards has helped inform and direct traffic, and because these devices are self-illuminated, they are much easier motorists to read. When you have the option of using them, always do so.
Other safety precautions to take in work zones to protect both employees and motorists include:
- Making certain that light towers are properly placed and aimed so as not to create blinding conditions for approaching vehicles.
- Arranging for a police presence, with flashing blue lights at the start of the work zone, will get motorists' attention, slowing them down in time for lane shifts or closures.
- Providing additional work zone controls, such as limiting work hours (for example, avoidance of lane closures on Fridays, weekends, Mondays or holidays), minimizing work starting hours on weekdays, and restricting work during special events.
In summary, work zone safety can be improved with a mixture of traditional and non-traditional methods, but the bottom line performance will be determined by enforcement of your safety practices. All workers on the site should understand the seriousness and urgency of making certain that safety rules and requirements are followed for the duration of the project.
John J. Meola, CSP, ARM, is a construction safety specialist in Richmond, VA. He is past president of the Colonial Virginia Chapter of the ASSE. He is the author of The Construction Safety Guide published by Genium Publishing, Schenectady, NY. His e-mail address is JMeola7755@aol.com.