Steel Erection Safety Rules May Be In For Historic Revision
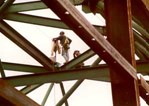
"And lo, the lion shall lie down with the lamb…though the lamb will not get much sleep." (old Woody Allen joke)
Statistically, steel erection accidents rank among the leading causes of death and injury in the construction industry, and the Occupational Safety and Health Administration (OSHA) wants something done about it. (In truth, most workers are far more at risk simply driving to and from work than they are on the job, but that's an entirely different subject!)
Of course, anytime OSHA tries to change something there's a collective howl from special interest groups. So this time, considering the complexity and hazards of steel erection, OSHA decided to invite a group of interested parties to "negotiate" safety improvements—and preserve enough flexibility in the final rules for erectors and contractors to remain productive. The name of this effort is the Steel Erection Negotiated Rulemaking Advisory Committee or "SENRAC".
SENRAC was composed of unions, erectors, general contractors, trade associations, steel fabricators and equipment suppliers, and others with direct involvement in steel fabrication and erection. Through a lengthy process of meetings, "give and take" sessions and review of technical specifications with all parties, a new set of steel erection safety standards was hammered out.
Getting Started
On large construction sites, the lead trade is typically the ironworkers. They generally set the relative standard for safety on a job—something every worker on a site will admit—and OSHA has finally recognized this.
Improved fall protection for ironworkers and others was clearly an important objective in the new rules, but no less important are crane and rigging operations, site controls, steel fabrication and erection techniques, fastener technology, and employee training. The committee also worked up language for "responsibility and accountability" for certain critical applications, such as column anchor bolts, concrete strengths, and steel assembly integrity. Too many accident investigations found "not my job" as the lame excuse for non-conveyance of critical safety information.
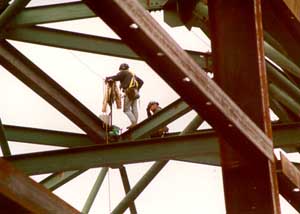
Keep in mind when reading the new proposal that OSHA and the committee reviewed a long history of construction accidents and "near misses" in compiling this standard. The details and elements addressed are intended to eliminate or control the most common hazards found in steel erection accident investigations. The committee was very thorough in their deliberations.
As with most regulatory provisions, many of the new rules are riddled with exceptions. By providing ‘alternate' means of assuring equivalent protection, the committee is trying to maintain the highly desirable attribute of ‘flexibility'. But take note, using the alternate provisions offered in the proposal requires additional documentation and records, planning, engineering appraisals, and approvals, and in general demand a lot more effort than complying with the regulations in their initial form.
The Regulations
Major sections are reviewed here in roughly the order they appear in the final proposal. Numerous details, alternate provisions, and references to Appendices are contained throughout the text. If you're in the steel business, you should read the complete proposal very closely. Visit the OSHA web site (http://www.osha.gov) for the latest update.
1926. 751: Definitions: Clarifying trade terminology. It's important to start with a full understanding of terms and meanings. Several key interpretations are established.
1926.752: Site layout controls: Contractors must provide certain information to erectors about minimum concrete strengths and repairs to anchor bolts; provisions are made for site layout responsibility, including access roads, graded and drained storage and machine set-up areas and pre-planned overhead protection details.
Many site laydown and staging areas are fraught with hazards, and often receive only a cursory safety evaluation. Pre-planning activity starts out here!
Site-specific erection plan: If an employer decides they cannot comply with the SENRAC regulations as written, they may choose to develop an "alternate" plan for providing employee protection, as long as it meets some very strict criteria. For example, it must be developed by a "qualified person," and "be available at the work site." Appendix A of the proposal gives guidelines for "alternate" plans.
1926.753: Hoisting and rigging: Major provisions include: recorded pre-shift visual crane inspection; operators authority is defined for handling loads; riding the headache ball is prohibited; controls for hoisting employees on personnel platforms; requirements for safety latches; prohibitions against working under suspended loads.
"Multiple lift rigging procedure":
- "Christmas trees" are allowed under controlled conditions, such as: maximum of five structural members hoisted at one time.
- Riggers and connectors receive specific training.
- 5-to-1 safety factor on hoisting and rigging gear.
- Crane capacity requirements are referenced.
- Seven-foot minimum distance required between hoisted members.
- Controlled lowering of load when over connectors.
1926.754: Structural steel assembly: Several new or modified provisions including: structural stability requirements; erection floor must not be more than eight stories above top most permanent floor in most cases; decked floor or nets within two stories or 30 feet of erection floor.
Also in this section:
- Controls over installation of shear connectors (stud weldments) to avoid creating tripping hazards.
- Prohibition of shear connectors in controlled decking zone (CDZ).
CDZ are permitted, but require careful set up and monitoring. Read the proposal closely for how they may be used. Since open, unprotected edges are allowed, the proposal correctly specifies no shear connectors, which are the cause of many trips and fall accidents.
Also addressed is the slipperiness of painted or coated structural steel. Steel must not be more slippery after painting than its original surface. The ASTM method for determining coefficients of friction is contained in an appendix. Steel suppliers will likely have additional comments on this provision, but it's always been a tough situation for the connectors and hopefully an equitable resolution can be reached.
Other provisions in this section include:
- Controls over plumbing up.
- Securing guy wire connections.
- Approvals needed before removing plumbing up cables.
- Prohibition against using decking bundle strapping for hoisting unless designed for this purpose. Good rigging practices are required for handling all loads and use of deck bundle strapping for lifting is prohibited.
Roof, floor and column openings must be covered or protected during decking. This has long been a source of a lot of accidents, not only to ironworkers, but roofers, sheet metal and masonry trades, and others. OSHA found that a lot of accidents happen when workers fall through a roof or floor. Additional controls are proposed for weight distribution on derrick floors.
1926.755: Anchor bolts:
- All columns must have at least four bolts meeting minimum strength requirements.
- Stability of columns is referenced.
- Anchor bolt repairs require structural engineer review, with written notification to erector of repairs to anchor bolts.
This section is important because OSHA and the committee found that field repaired or modified anchor bolts have caused accidents in many cases. This provision is intended to standardize field repairs and requires notification to the erector.
1926.756: Beams and Columns: Loads shall not be released from the hoist line until members are secured with at least two bolts per connection. Solid web members used as diagonal bracing must be secured with at least one bolt. This provision addresses the historic practice of single bolting, a troublesome point of contention between the steel erection community and OSHA.
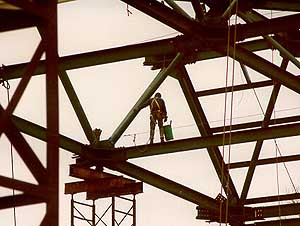
Double connections at columns and/or beam webs over a column: At least one bolt must be used or a shop-attached or field-bolted seat or similar connection device must be used to prevent displacement. The intent here is to use additional hardware on columns. Reliance on gravity and friction to hold steel in place is being replaced with bolts or hardware.
Also in this section:
- Minimum strengths of column splices.
- Perimeter columns must extend at least 48 inches above finished floors to allow attachment of perimeter safety cables.
- Perimeter safety cables shall be installed.
- Cables must be minimum of ½ inch wire rope or equivalent, 42–45 inches above finished floor.
- The fabricator/supplier will provide holes or other devices on perimeter columns that permit attachment of safety cables.
Remember how nuts or heavy washers were tack-welded onto columns for attaching safety cables? The proposal seeks to improve this dangerous task since welders are required to be at or near an unprotected edge to do this.
The committee wants to shift the responsibility for compliance upstream in the fabrication process. While this sounds like a good idea, it's likely to generate premature hair loss among suppliers. By including fall protection elements into design criteria, a lot of guesswork and field invention is eliminated. This is a welcome development, although the industry will have to adjust.
It's worth noting that technology can play an increasingly vital role in making steel erection safer. For example, advanced computer-aided design (CAD) software allows designers to make these additions with relative ease, and the fall protection hardware manufacturers haven't failed yet to come up with innovative solutions to tough fall protection problems.
1926.757: Open Web Steel Joists
- Shall be field bolted at or near columns to provide lateral stability.
- Where joists at or near columns are 60 feet or less, they shall have minimum strength to allow one employee to release the hoist line without erection bridging.
- On joists over 60 feet, they must be set in tandem with all bridging installed, unless it can be done more safely and you can prove it in your site-specific plan.
- Stabilizer plates must be provided on each column, extending at least three inches below the bottom chord, and have a 13/16 inch hole for attaching plumbing up cables.
This has been another problem area for ironworkers and the committee is trying to address this with a uniform fix. They don't mention if "equivalent means" are acceptable, such as use of a clamp or other attachment. The intent is to replace the questionable practice of wrapping a choker cable around a column and hoping it grabs and holds.
- When joists are landed on a structure, they must be secured against displacement.
It should be obvious by now that many of the new requirements are aimed at securing pieces during the erection process. These are ‘weak spots' in the erection process, where steel may be placed free-standing or self-supported, and subject to displacement and falling. Achieving compliance will require changes in traditional ironworker trade practices—changes that can be made easier by better safety planning and coordination, beginning in the fabricators drafting loft.
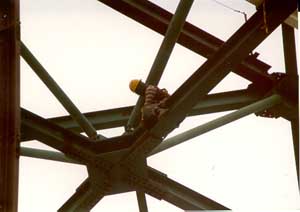
Additional provisions include:
- Joists hung in bays spanning over 40 feet must be fabricated to allow for field bolting.
- Joists and girders may not be used as anchorage points for fall protection unless written direction is given from a qualified person.
- No modification affecting joist strength can be made without approval of project engineer.
- Minimum weld and bolt sizes are referenced for attaching joists.
- Landing of bundles of bridging or decking on joists is controlled.
The proposal directs new regulations at hanging joists, depending upon their span and configuration. Employee access to joists is restricted with certain provisions. Generally some form of joist bracing or attachment must be made before the hoist line is released.
1926.758 : Pre-engineered metal buildings
- A site layout plan must be completed before steel erection can begin.
- Columns require at least four anchor bolts.
- Rigid frames must have a specified number of bolts tightened on each side of web before hoist line is released.
- Provisions in this section include controls for use of purlins or girts as walking surfaces or anchorage points.
1926.759 : Falling object protection
- Loose items aloft must be secured.
- No construction activity permitted beneath steel erection unless adequate falling object protection is provided.
1926.760: Fall Protection:
- Generally, some form of fall protection is required at 15 feet.
- Fall protection includes: safety cables, guardrails, nets, personal fall arrest, and restraints. These are the same methods and devices from existing OSHA construction fall protection standards.
- Connectors are required to have some form of fall protection when working above 30 feet and must be trained in correct use of fall protection. Over 15 feet up to 30 feet, connectors must be provided with and wear fall protection gear "to be able to be tied off."
Controlled Decking Zone (CDZ)
- Employees working at leading edges in CDZ's must have fall protection against a fall of two stories or 30 feet.
- Limited CDZ access: only those employees doing leading edge work are allowed in the CDZ.
- Boundaries of CDZ must be clearly designated by use of control lines—not more than 90 feet wide or 90 feet deep from any leading edge.
- Employees working in the CDZ must have fall hazard awareness and fall prevention training.
- Final deck attachments and shear connectors shall not be installed in the CDZ because they present tripping hazards.
- Use of covers and protection of openings and holes is specified.
- Custody of fall protection such as perimeter cables and safety lines shall remain in an area to be used by other trades.
Training
Fall Hazard training must be provided by a qualified person. Training must include:
- Recognition and identification of fall hazards.
- Use of fall protection equipment and methods: perimeter safety cables, harnesses, restraints, nets, controlled decking zones, etc.
- Correct methods to install, use, maintain, disassemble, and inspect fall protection systems.
- Methods of preventing falls through holes and openings.
- Special fall protection training is required for riggers and connectors performing multiple lifts (Christmas treeing).
Summary: This new proposal represents a noble effort on the part of SENRAC and OSHA, and it merits the support of all parties to move toward adoption. OSHA has tried a new approach to solving a tough problem, and it represents the best attempt thus far at providing a workable set of standards to the steel erection community.
The formal comment period in now closed and the proposal is working its way through the rulemaking approval process. While this is happening it's a good idea to become familiar with the new provisions since they make a lot of "safety sense" whether they're adopted or not. OSHA's Website can be found at http://www.osha.gov.
The final version of SENRAC is now going through a lengthy formal approval process in Washington and is anticipated to emerge as a final rule sometime late this year. Since OSHA has tried a cooperative approach with this new rulemaking process, there's a lot riding on its success and adoption.
BIO: John J. Meola, CSP, ARM, is a construction safety specialist and past president of the Colonial Virginia Chapter of the ASSE in Richmond, VA. JMeola7755@aol.com.