Team Management Keeps Family-Owned Alu-Bra Foundry On Top Of Safety
Jim Torkelson took over the Alu-Bra Foundry Inc., in Bensenville IL, in 1991 after the death of his father, Emmett, who had owned and operated the foundry since 1960. Jim was joined on the management team by his wife, Kim, after their marriage in 1993. Jim runs the foundry operations while Kim administers human resources and worker safety.
Alu-Bra makes brass, bronze, and aluminum sand castings for products weighing from a few ounces up to 500 pounds. It offers its customers engineering and design services as well as prototype and production casting runs, heat treating and finishing. Alu-Bra serves a wide variety of industries but specializes in parts for fluid pumps and valves for water works.
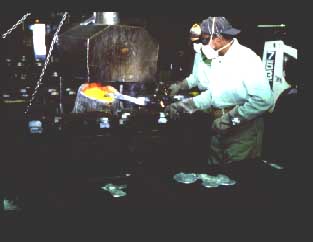
Because Alu-Bra workers are exposed to lead in the casting operation and silica in the molding operation, the company is concerned with protecting their health from airborne contaminants. When the owners found that some employee blood lead levels exceeded the action level under Occupational Safety and Health Administration (OSHA) rules, they initiated immediate steps to reduce blood lead levels.
Those steps included some major renovations to the plant and installation of engineering controls to remove dust and fumes from the air in particularly troublesome areas. They also initiated a comprehensive respirator program based on good industrial hygiene principles to educate workers about the effects of airborne contaminants on their health and the importance of respirators to help protect them at work.
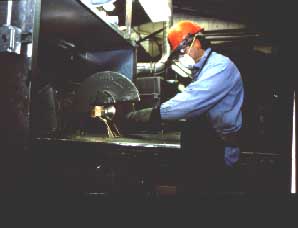
Plant Renovation
The plant renovation began in 1994 when Alu-Bra retained a foundry consultant to help evaluate which work areas needed additional ventilation controls. Ventilation systems were installed at the molding lines at the front of the foundry, at the center of the building near the grinding shop and in the cleaning room. The renovations, which also included new office space and new heating for the foundry area, were complete in 1998.
In the end, the price tag was high and the disruptions were many. "It involved taking down about half the building and expanding 60 feet, rebuilding around the old building," says Jim Torkelson.
Even with the plant improvements and the new ventilation systems in place, the Torkelsons continue to educate workers on the importance of respiratory protection, and workers use respirators in most production areas. Because worker exposure levels are below OSHA's PEL for lead, respirators are no longer legally required for employees in the grinding and molding areas. But Alu-Bra requires these workers to wear them because they move through other areas in the foundry where respirators are required. (Note: OSHA's lead standard requires an employer to provide a respirator to an employee who requests one, even if exposure levels are below the PEL).
Management of Respiratory Protection Program
Alu-Bra management has continued to emphasize the importance of appropriate respiratory protection, using posters, videos and annual fit testing as opportunities to underscore good worker safety procedures.
Fit testing is accomplished with a fit-testing package from 3M, since the plant uses the 3M Model 8511 and Model 8210 particulate respirators for most applications. Employees prefer these maintenance-free respirators because they are lightweight, comfortable, and easy to use. Alu-Bra also uses the 3M Compliance Software to manage its respiratory protection program, which Kim Torkelson customizes to suit Alu-Bra's specific requirements.
Kim Torkelson receives reports every six months from an occupational health clinic, and Alu-Bra's wide-ranging efforts to reduce blood lead levels has paid off, as these reports show that workers' average blood lead levels continue to decline. "All the renovations helped, but what really made the difference was their use of the maintenance-free respirators," she says, as well as management encouraging workers to "keep their face and hands clean."
Alu-Bra selected maintenance-free respirators because workers prefer their light weight, comfort and ease of use. Torkelson likes them because they are cost-effective, and she says their ease of use makes the company's respirator program easier to administer. "Maintenance-free respirators are the best option for us."
For more information about respiratory protection, contact 3M Occupational Health and Environmental Safety Division at 651-733-1110.